Complaint Review: Prosource - Jacksonville Florida
- Prosource 5250 Sunbeam Rd Jacksonville, Florida United States of America
- Phone: 904-288-5688
- Web:
- Category: Building Products
Prosource They do not warranty the products they sell. Jacksonville, Florida
*UPDATE Employee: When Wood Gets Wet it is Ruined
*UPDATE Employee: ProSource Response
*UPDATE Employee: ProSource fully supports all manufacturer warranties on every product we sell.
*UPDATE Employee: ProSource fully supports all manufacturer warranties on every product we sell.
*Author of original report: Prosource is the one who stated that the flooring be glued!
*General Comment: No, Not installed correctly
listed on other sites?
Those sites steal
Ripoff Report's
content.
We can get those
removed for you!
Find out more here.
Ripoff Report
willing to make a
commitment to
customer satisfaction
Click here now..
They do not warranty their products!
Company relationship started out good, now that I have a warranty issue, it's sorry it's your problem!
Here are the details on my hardwood flooring problem:
Seven months ago we bought from Prosource 1000 sq ft Amendoim engineered (1/2 x 5) hardwood flooring.
About 1 month ago we noticed certain blanks and areas turning black almost burnt looking, also about 60% of the finish looks slightly wrinkled following the wood grain. My wife noticed this 1 month after installation. There some knots in the wood appear to have swollen.
The dark areas (6 blanks in formal dining room, none in living room, 10-12 blanks in den, 1 blank in hall and none in master bed room) are not near windows.
Prosource came out and had to return later since he didn't have a moisture meter and said we had a severe moisture problem coming from the concrete. They said this (moisture) is not covered under warranty and that I should call my insurance company. Also that even if it had been checked for moisture that was only good for that moment in time, not later when I have a problem. So no matter what it was my problem.
There are no water leaks, that has been checked. We havent had much rain this year.
The house is brick and 34 years old, the carpet was removed, molding and concrete vacuumed clean, there were no cracks, mold or mildew stains on the concrete, molding or carpet that was removed. The flooring sat in the house for 3 weeks before Ron could install. So it was acclimated.
We have a dehumidifier in the home and it is set at 50%. We had a couple walls opened up as part of our remodeling bathrooms and there was no mold or dampness in the walls.
So according to them, moisture is coming thru the concrete, the glue (a moisture barrier), and is ruining my floor.
Maybe the wood wasn't properly Kiln dried and still had moisture trapped inside!
This report was posted on Ripoff Report on 02/27/2012 07:39 AM and is a permanent record located here: https://www.ripoffreport.com/reports/prosource/jacksonville-florida-32257/prosource-they-do-not-warranty-the-products-they-sell-jacksonville-florida-845183. The posting time indicated is Arizona local time. Arizona does not observe daylight savings so the post time may be Mountain or Pacific depending on the time of year. Ripoff Report has an exclusive license to this report. It may not be copied without the written permission of Ripoff Report. READ: Foreign websites steal our content
If you would like to see more Rip-off Reports on this company/individual, search here:



#6 UPDATE Employee
When Wood Gets Wet it is Ruined
AUTHOR: GET YOUR STUFF TOGETHER!!! - (United States of America)
SUBMITTED: Monday, April 02, 2012
Wood is a naturally occurring material. If wood gets wet it gets damaged. As such, wood products are never warrantied against moisture. Moisture is water. If you have water permeating up through your concrete slab it will damage your wood.
It is the responsibility of your flooring installer to check for moisture on the concrete slab before he installs wood, laminate or tile. And that situation will change depending on the time of year, the rainfall level and the ever changing water table.
Moisture can also affect your wood if your house is not climate controlled year round. That means maintaining a relative humidity level between 35% to 55%. If your thermostat is set at 77 or 78 degrees, you would have a relative humidity level of 55%
Before you purchase wood flooring or tile products educate yourselves so that you do not end up making costly mistakes.

#5 UPDATE Employee
ProSource Response
AUTHOR: ProSource - (United States of America)
SUBMITTED: Wednesday, February 29, 2012
ProSource of Jacksonville has been in business servicing the Jacksonville community for nearly 19 years. Our company has built a very strong reputation for providing only first quality products at the guaranteed lowest prices directly to the Trades Professionals and their clients. At ProSource, our goal is to provide our customers with exceptional service, both before and after the sale. An unfortunate reality for any business, in any industry, is that sometimes a customer may experience a problem with a product they purchased. When this occurs, ProSource makes every reasonable effort to resolve the issue to the customers satisfaction. In response to this customers complaint:
It is very important to understand that ProSource does not produce/make/manufacturer the products we sell. As with any product made in any industry, it is always the actual manufacturer that sets and administers the warranty guidelines on their products. The customer states that ProSource does not warranty the products they sell, this statement is simply not correct. ProSource fully supports all manufacturer warranties on every product we sell.
The situation the customer is having is caused by moisture. As the customer mentions, a ProSource representative, as well as a representative from the hardwood manufacturer, visited the home and took moisture readings of the floor using a standard moisture meter. The readings showed extremely high moisture content in the floor; far greater than the industry standard allowable moisture tolerances. The customer states Maybe the wood was not properly kiln dried and still had moisture trapped inside. While all hardwood products contain a degree of moisture, the purpose of acclimation before the installation process is to allow time for the moisture content of the hardwood to match the relative humidity of the installation environment. A standard acclimation period for hardwood flooring is 72 hours; the customer states in his report that he let the wood acclimate for three weeks. With that being the case, it becomes inconceivable to think that the hardwood flooring would contain excess moisture that was not already present in the home, regardless of how it was dried during production.
It is also very important to state that the customer hired his own installer to perform the installation of the hardwood. Neither ProSource, nor a ProSource recommended installer were involved in the installation process in any way. During the jobsite inspection, a ProSource representative spoke with the installer whom the customer hired to perform the work. When asked about the moisture content of the subfloor prior to the installation, the installer stated that he did not perform any type of moisture testing prior to the installation. Performing this type of test is considered to be an industry standard practice and is absolutely required by every hardwood manufacturer to maintain warranty on their products, and frankly, to prevent situations like this from occurring. Not only is this type of testing required by the hardwood manufacturers, it is also required by all adhesive manufacturers and is printed directly on each pail of adhesive that the installer would have used during the installation. While the customers comment about the adhesive acting as a moisture barrier is correct to a point, the adhesive used is not designed to withstand excessive moisture, nor should it have been applied if excessive moisture was present in the subfloor.
The facts surrounding this situation are clear; the customers subfloor has excessive moisture. This can be caused by a number of variables which can easily be researched by simply searching concrete subfloor moisture on the internet. This is a common issue, especially in Florida, and there are several products on the market which can be used to correct this. However, the proper testing was not done prior to the installation of the hardwood, so this excessive moisture condition was not detected, nor resolved. This excessive moisture is now being absorbed by the hardwood causing discoloration and also causing the product to swell, which affects the finish coating as described in the customers report. As with any type of flooring, proper installation is required by the manufacturer to maintain warranty on the product. Unfortunately in this situation, the product was not installed properly according to industry standards, nor was it installed in compliance with the hardwood manufacturer or the adhesive manufacturer guidelines. Furthermore, excessive moisture in the subfloor is not a condition related to the manufacturing process of the hardwood, and therefore is not considered to be a manufacturing defect. For these reasons, the manufacturer of the hardwood has denied responsibility for the issue.
While this situation is unfortunate, as ProSource was not involved in the installation of the hardwood, and considering the proper installation procedures were not followed, it is ProSources position that we do not have responsibility for the issue. However, in fairness and goodwill towards our customer, we are more than willing to provide replacement product, including the proper moisture control products, to the customer at a substantial reduction in price. We will also be happy to help the customer find an installer who will follow the proper installation guidelines so the issue does not continue. While ProSource cannot be responsible for issues which we did not create, we will do what we can to help this customer in other ways to reduce their out of pocket expense while correcting the issue. We do hope the customer will realize that ProSource has treated him fairly in this situation, and that we remain here to assist him however possible.

#4 UPDATE Employee
ProSource fully supports all manufacturer warranties on every product we sell.
AUTHOR: ProSource of Jacksonville - (United States of America)
SUBMITTED: Wednesday, February 29, 2012
ProSource of Jacksonville has been in business servicing the Jacksonville community for nearly 19 years. Our company has built a very strong reputation for providing only first quality products at the guaranteed lowest prices directly to the Trades Professionals and their clients. At ProSource, our goal is to provide our customers with exceptional service, both before and after the sale. An unfortunate reality for any business, in any industry, is that sometimes a customer may experience a problem with a product they purchased. When this occurs, ProSource makes every reasonable effort to resolve the issue to the customers satisfaction. In response to this customers complaint:
It is very important to understand that ProSource does not produce/make/manufacturer the products we sell. As with any product made in any industry, it is always the actual manufacturer that sets and administers the warranty guidelines on their products. The customer states that ProSource does not warranty the products they sell, this statement is simply not correct. ProSource fully supports all manufacturer warranties on every product we sell.
The situation the customer is having is caused by moisture. As the customer mentions, a ProSource representative, as well as a representative from the hardwood manufacturer, visited the home and took moisture readings of the floor using a standard moisture meter. The readings showed extremely high moisture content in the floor; far greater than the industry standard allowable moisture tolerances. The customer states Maybe the wood was not properly kiln dried and still had moisture trapped inside. While all hardwood products contain a degree of moisture, the purpose of acclimation before the installation process is to allow time for the moisture content of the hardwood to match the relative humidity of the installation environment. A standard acclimation period for hardwood flooring is 72 hours; the customer states in his report that he let the wood acclimate for three weeks. With that being the case, it becomes inconceivable to think that the hardwood flooring would contain excess moisture that was not already present in the home, regardless of how it was dried during production.
It is also very important to state that the customer hired his own installer to perform the installation of the hardwood. Neither ProSource, nor a ProSource recommended installer were involved in the installation process in any way. During the jobsite inspection, a ProSource representative spoke with the installer whom the customer hired to perform the work. When asked about the moisture content of the subfloor prior to the installation, the installer stated that he did not perform any type of moisture testing prior to the installation. Performing this type of test is considered to be an industry standard practice and is absolutely required by every hardwood manufacturer to maintain warranty on their products, and frankly, to prevent situations like this from occurring. Not only is this type of testing required by the hardwood manufacturers, it is also required by all adhesive manufacturers and is printed directly on each pail of adhesive that the installer would have used during the installation. While the customers comment about the adhesive acting as a moisture barrier is correct to a point, the adhesive used is not designed to withstand excessive moisture, nor should it have been applied if excessive moisture was present in the subfloor.
The facts surrounding this situation are clear; the customers subfloor has excessive moisture. This can be caused by a number of variables which can easily be researched by simply searching concrete subfloor moisture on the internet. This is a common issue, especially in Florida, and there are several products on the market which can be used to correct this. However, the proper testing was not done prior to the installation of the hardwood, so this excessive moisture condition was not detected, nor resolved. This excessive moisture is now being absorbed by the hardwood causing discoloration and also causing the product to swell, which affects the finish coating as described in the customers report. As with any type of flooring, proper installation is required by the manufacturer to maintain warranty on the product. Unfortunately in this situation, the product was not installed properly according to industry standards, nor was it installed in compliance with the hardwood manufacturer or the adhesive manufacturer guidelines. Furthermore, excessive moisture in the subfloor is not a condition related to the manufacturing process of the hardwood, and therefore is not considered to be a manufacturing defect. For these reasons, the manufacturer of the hardwood has denied responsibility for the issue.
While this situation is unfortunate, as ProSource was not involved in the installation of the hardwood, and considering the proper installation procedures were not followed, it is ProSources position that we do not have responsibility for the issue. However, in fairness and goodwill towards our customer, we are more than willing to provide replacement product, including the proper moisture control products, to the customer at a substantial reduction in price. We will also be happy to help the customer find an installer who will follow the proper installation guidelines so the issue does not continue. While ProSource cannot be responsible for issues which we did not create, we will do what we can to help this customer in other ways to reduce their out of pocket expense while correcting the issue. We do hope the customer will realize that ProSource has treated him fairly in this situation, and that we remain here to assist him however possible.

#3 UPDATE Employee
ProSource fully supports all manufacturer warranties on every product we sell.
AUTHOR: ProSource of Jacksonville - (United States of America)
SUBMITTED: Wednesday, February 29, 2012
ProSource of Jacksonville has been in business servicing the Jacksonville community for nearly 19 years. Our company has built a very strong reputation for providing only first quality products at the guaranteed lowest prices directly to the Trades Professionals and their clients. At ProSource, our goal is to provide our customers with exceptional service, both before and after the sale. An unfortunate reality for any business, in any industry, is that sometimes a customer may experience a problem with a product they purchased. When this occurs, ProSource makes every reasonable effort to resolve the issue to the customers satisfaction. In response to this customers complaint:
It is very important to understand that ProSource does not produce/make/manufacturer the products we sell. As with any product made in any industry, it is always the actual manufacturer that sets and administers the warranty guidelines on their products. The customer states that ProSource does not warranty the products they sell, this statement is simply not correct. ProSource fully supports all manufacturer warranties on every product we sell.
The situation the customer is having is caused by moisture. As the customer mentions, a ProSource representative, as well as a representative from the hardwood manufacturer, visited the home and took moisture readings of the floor using a standard moisture meter. The readings showed extremely high moisture content in the floor; far greater than the industry standard allowable moisture tolerances. The customer states Maybe the wood was not properly kiln dried and still had moisture trapped inside. While all hardwood products contain a degree of moisture, the purpose of acclimation before the installation process is to allow time for the moisture content of the hardwood to match the relative humidity of the installation environment. A standard acclimation period for hardwood flooring is 72 hours; the customer states in his report that he let the wood acclimate for three weeks. With that being the case, it becomes inconceivable to think that the hardwood flooring would contain excess moisture that was not already present in the home, regardless of how it was dried during production.
It is also very important to state that the customer hired his own installer to perform the installation of the hardwood. Neither ProSource, nor a ProSource recommended installer were involved in the installation process in any way. During the jobsite inspection, a ProSource representative spoke with the installer whom the customer hired to perform the work. When asked about the moisture content of the subfloor prior to the installation, the installer stated that he did not perform any type of moisture testing prior to the installation. Performing this type of test is considered to be an industry standard practice and is absolutely required by every hardwood manufacturer to maintain warranty on their products, and frankly, to prevent situations like this from occurring. Not only is this type of testing required by the hardwood manufacturers, it is also required by all adhesive manufacturers and is printed directly on each pail of adhesive that the installer would have used during the installation. While the customers comment about the adhesive acting as a moisture barrier is correct to a point, the adhesive used is not designed to withstand excessive moisture, nor should it have been applied if excessive moisture was present in the subfloor.
The facts surrounding this situation are clear; the customers subfloor has excessive moisture. This can be caused by a number of variables which can easily be researched by simply searching concrete subfloor moisture on the internet. This is a common issue, especially in Florida, and there are several products on the market which can be used to correct this. However, the proper testing was not done prior to the installation of the hardwood, so this excessive moisture condition was not detected, nor resolved. This excessive moisture is now being absorbed by the hardwood causing discoloration and also causing the product to swell, which affects the finish coating as described in the customers report. As with any type of flooring, proper installation is required by the manufacturer to maintain warranty on the product. Unfortunately in this situation, the product was not installed properly according to industry standards, nor was it installed in compliance with the hardwood manufacturer or the adhesive manufacturer guidelines. Furthermore, excessive moisture in the subfloor is not a condition related to the manufacturing process of the hardwood, and therefore is not considered to be a manufacturing defect. For these reasons, the manufacturer of the hardwood has denied responsibility for the issue.
While this situation is unfortunate, as ProSource was not involved in the installation of the hardwood, and considering the proper installation procedures were not followed, it is ProSources position that we do not have responsibility for the issue. However, in fairness and goodwill towards our customer, we are more than willing to provide replacement product, including the proper moisture control products, to the customer at a substantial reduction in price. We will also be happy to help the customer find an installer who will follow the proper installation guidelines so the issue does not continue. While ProSource cannot be responsible for issues which we did not create, we will do what we can to help this customer in other ways to reduce their out of pocket expense while correcting the issue. We do hope the customer will realize that ProSource has treated him fairly in this situation, and that we remain here to assist him however possible.

#2 Author of original report
Prosource is the one who stated that the flooring be glued!
AUTHOR: donzzzzzz - (United States of America)
SUBMITTED: Monday, February 27, 2012
Prosource sold the special glue for concrete floors with the wood flooring. The first question asked is do you want floating or glue down. The engineered floor was designed for gluing, not floating. In Florida you buy either floating or glue down, rare to nail down. They even stated that floating was not recommended!

#1 General Comment
No, Not installed correctly
AUTHOR: Bubba Lee - (Canada)
SUBMITTED: Monday, February 27, 2012
Any one in the flooring business knows it is a bad idea to install wood flooring on concrete. Claiming that glue is a moisture barrier is just lying. You should be suing the installer.
Not blaming the manufacturer.

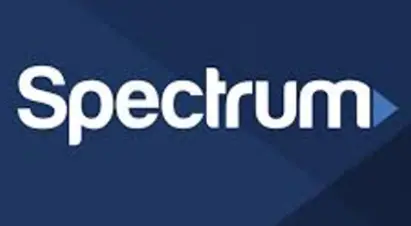
Advertisers above have met our
strict standards for business conduct.